Как делают поезда московского метро
Мы побывали на заводе «Метровагонмаш» и показываем процесс — от металлического листа до вагона
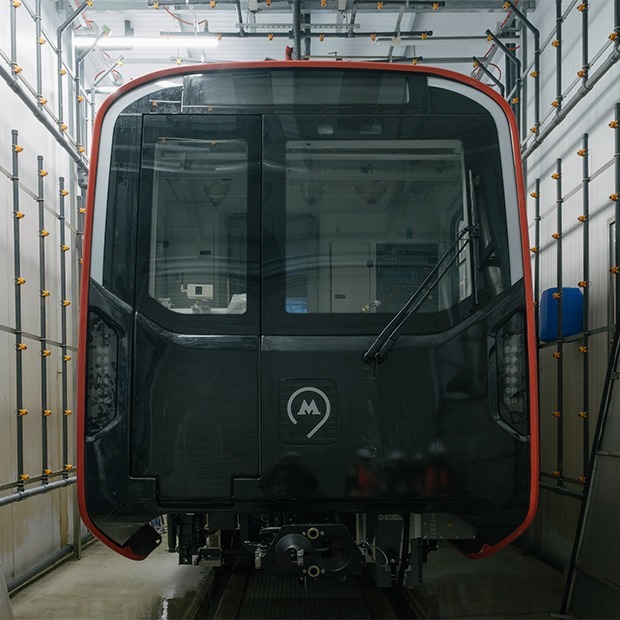
Совсем недавно на Замоскворецкой, зеленой ветке московского метро появились первые поезда «Москва-2024». От предыдущей версии «Москва-2020» они отличаются более утилитарным дизайном, удобным входом для маломобильных пассажиров и увеличенной вместимостью. Но все же нововведение, которое мы заметили первыми, — USB-зарядки перенесены с сидений на поручни. Пока в метро ходят 8 поездов «Москва-2024», но скоро их станет намного больше — новые составы уже собирают на заводе «Метровагонмаш» в подмосковных Мытищах.
Автор: Алина Калинина
Фотограф: Анастасия Пожидаева
Рельсовый транспорт в Мытищах производят с 1897 года: еще до революции здесь начали выпускать вагоны для железной дороги и трамваев. В советское время на заводе производили первые электрички и трамваи, а также самосвалы, прицепы для тракторов и легковых автомобилей. С 90-х завод полностью перешел на выпуск рельсовых автобусов и метровагонов — сейчас это вагоны для Москвы, Петербурга и других городов мира, а также рельсовый автобус, который эксплуатируется на неэлектрифицированных участках российских железных дорог.
Мы побывали на «Метровагонмаше» и рассказываем, как делают метропоезда.
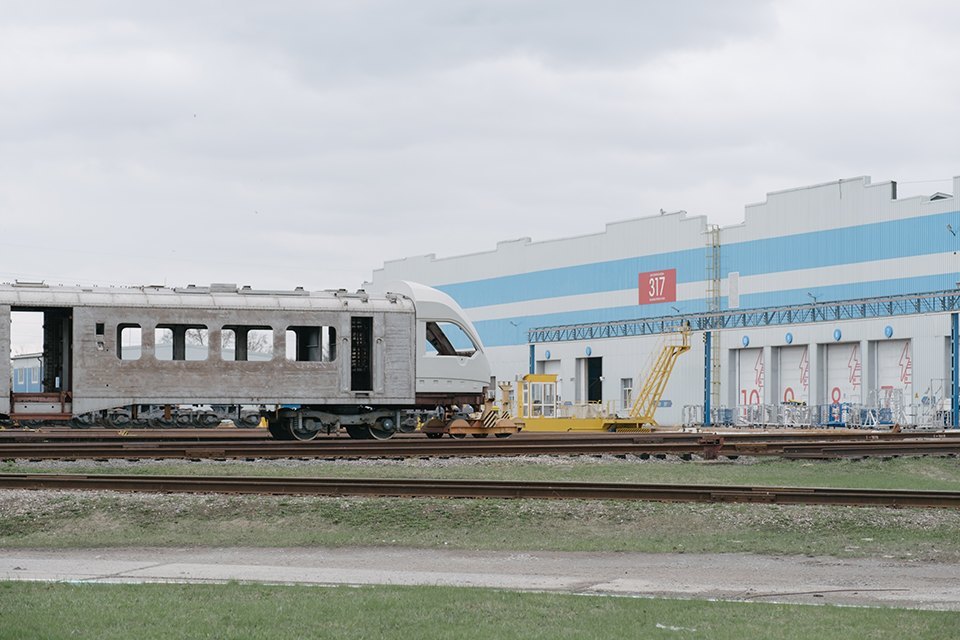
«Метровагонмаш»
Год основания:
1897
Продукция:
метровагоны, рельсовые автобусы
Количество сотрудников:
более 3 тысяч человек
Колыбель вагонов
Прессово-заготовительный цех, откуда начинается производство, на заводе называют «колыбелью вагонов». Сюда привозят листы металла, их раскраивают на детали и потом отправляют в другие цеха. Металл для вагона нужен разный, одни виды используются чаще, другие — реже, но все это нужно где-то хранить. Для этого в цехе есть специальная стапельная система — что-то вроде большого шкафа с движущимися полками, на каждой из которых лежат листы определенного вида. Хранится металл как в библиотеке: все виды внесены каталог, и оператор просто опускает полку с тем, что ему нужно. Разместить в этом шкафу одновременно можно до 32 сортов металла. Так его проще искать и доставать, а листы не занимают место на полу.
В цехе есть станки резки двух видов — с шестиметровым или трехметровым столом. Это позволяет раскраивать практически все детали, даже крупные, используемые для кузова вагона. Для крупных деталей используют плазменную резку — детали помещают в емкость с жидкостью, где их разрезают иглой с горящим наконечником. Для мелких — до десяти миллиметров — деталей нужна лазерная резка.
Для одних конструкций используют лазерную или плазменную резки, а для других — резку на прессе. Все зависит от нужного количества деталей: с помощью лазерной резки одну деталь можно получить за десять секунд, а пресс штампует ее за две секунды. Если это детали массового производства, которые нужны десятками тысяч, их нарезают с помощью прессов.
После термической резки металл может быть неровным, так что он отправляется в листоправильную, или же на участок гибочных прессов. Здесь тоже трудится роботизированная рука, которая сгибает детали весом больше ста килограммов.
В прессово-заготовительном цехе работают не только с металлом: также здесь есть установки для нарезки фанеры, оргстекла, ткани и резины. Все готовые детали отправляются в «Супермаркет» — склад контролируемых запасов, который находится в этом же цехе. В каждой ячейке лежат определенные запчасти, и это отражается в системе «1С». Когда появляется потребность в деталях, комплектовщик получает уведомление на планшете и сразу видит номер ячейки, номер детали и тару, в которую ее нужно упаковать. Информация о каждой детали, которая попадает в «Супермаркет» или уже пошла в дело, записывается на RFID-чип, так что бумажные накладные не нужны.
Сотрудников в этом цехе немного — почти все операции автоматизированы. Например, оператор аппарата лазерной сварки только следит за процессом с пульта управления. Заходить в камеру запрещено, так что там с деталью работают роботизированные руки. В этом аппарате изготавливают внешнюю часть боковины вагона. Поскольку она обращена к пассажирам, дефекты на ее поверхности недопустимы. И лазерная сварка как раз помогает избежать прожогов.
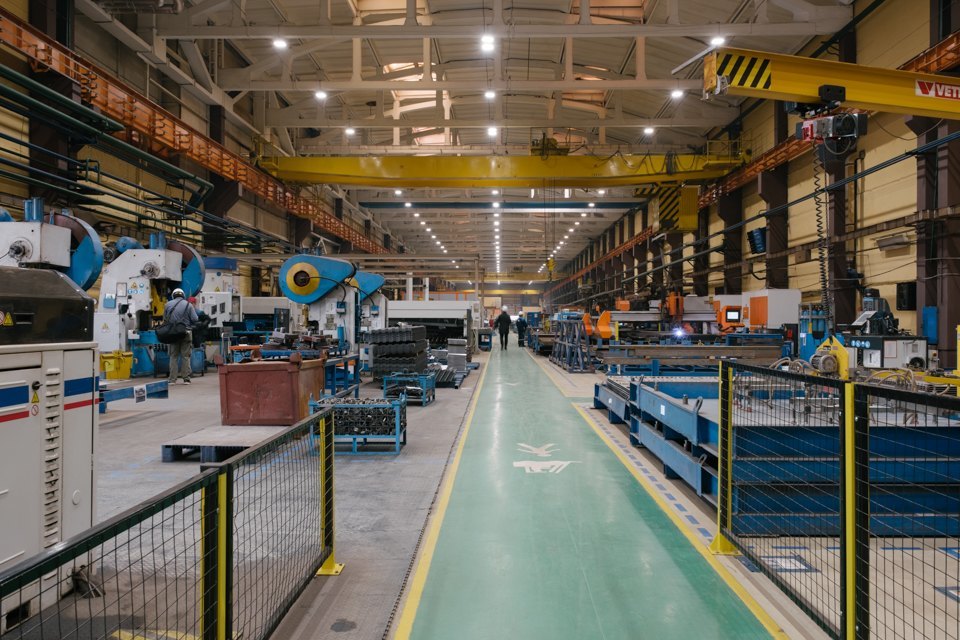
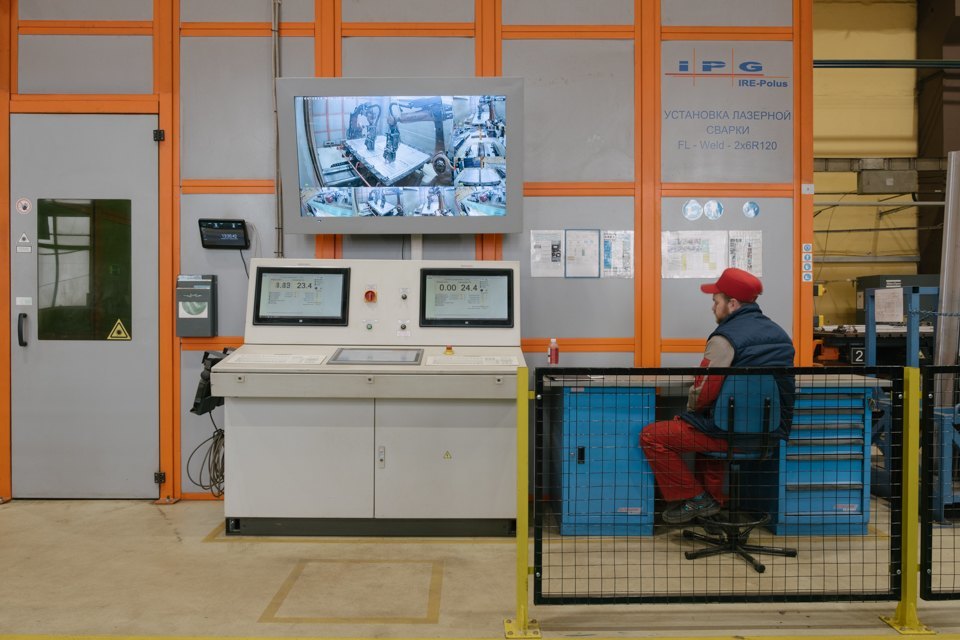
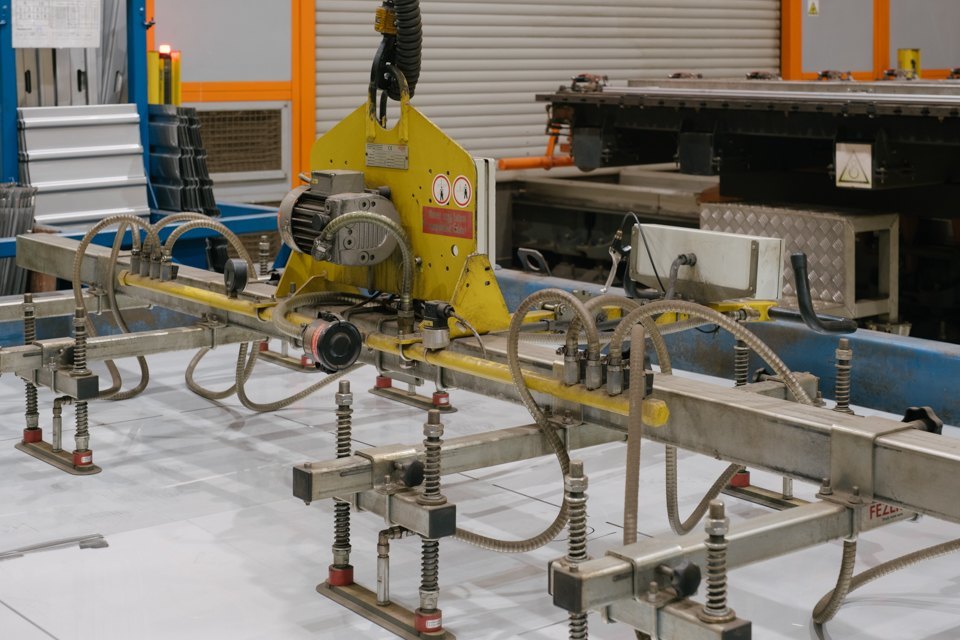
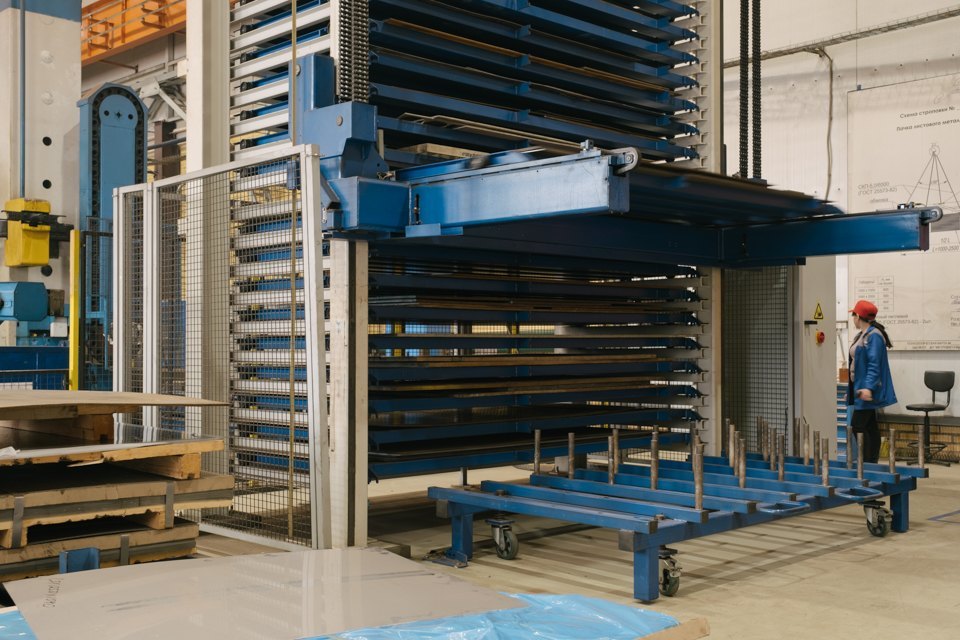
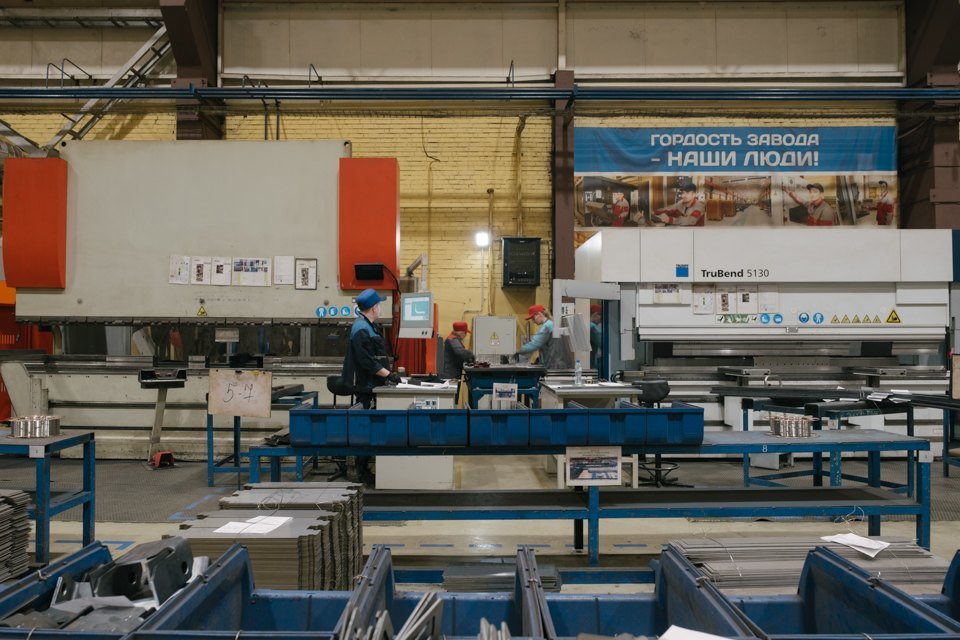
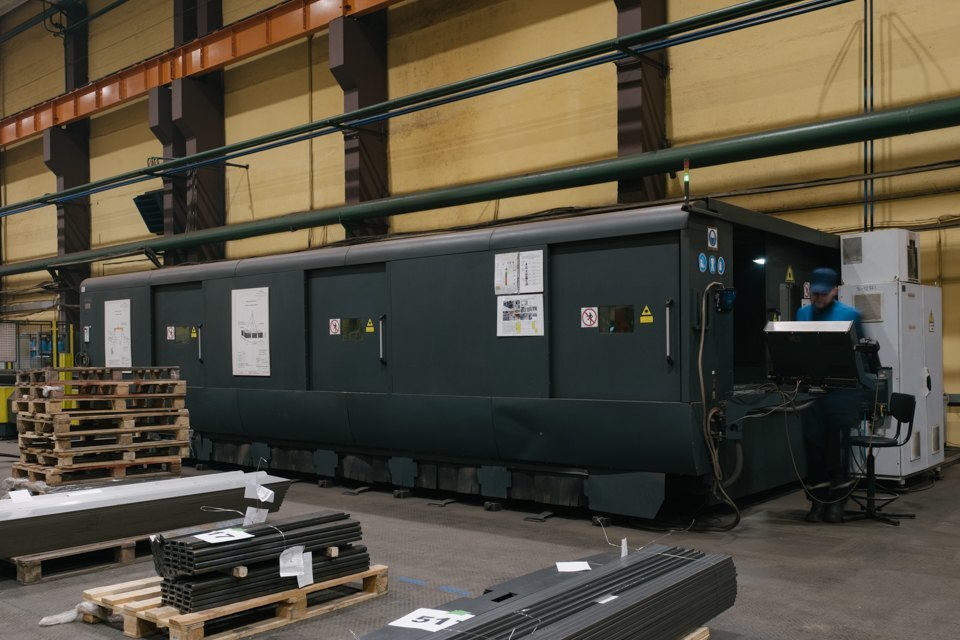
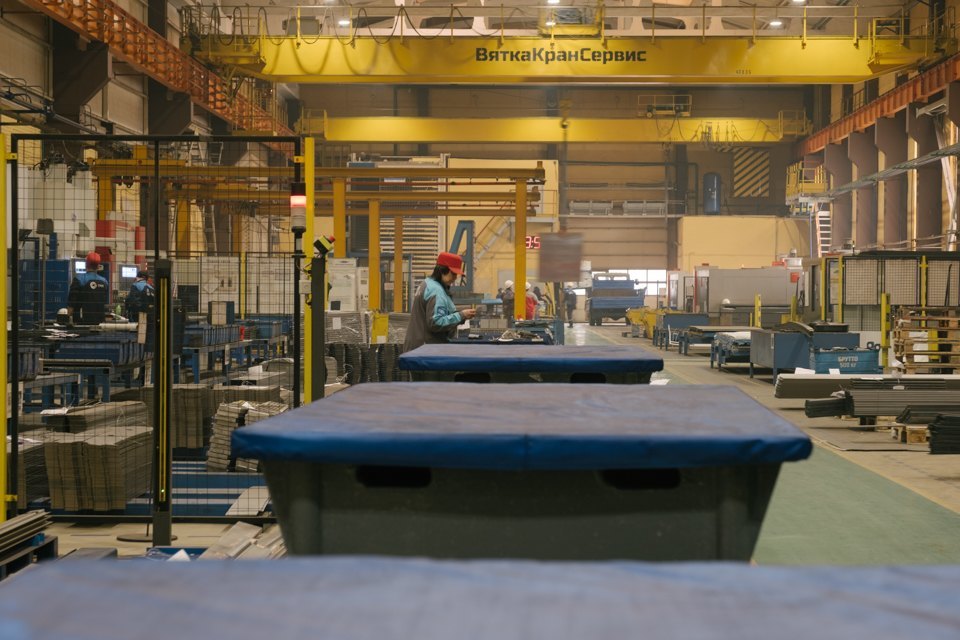
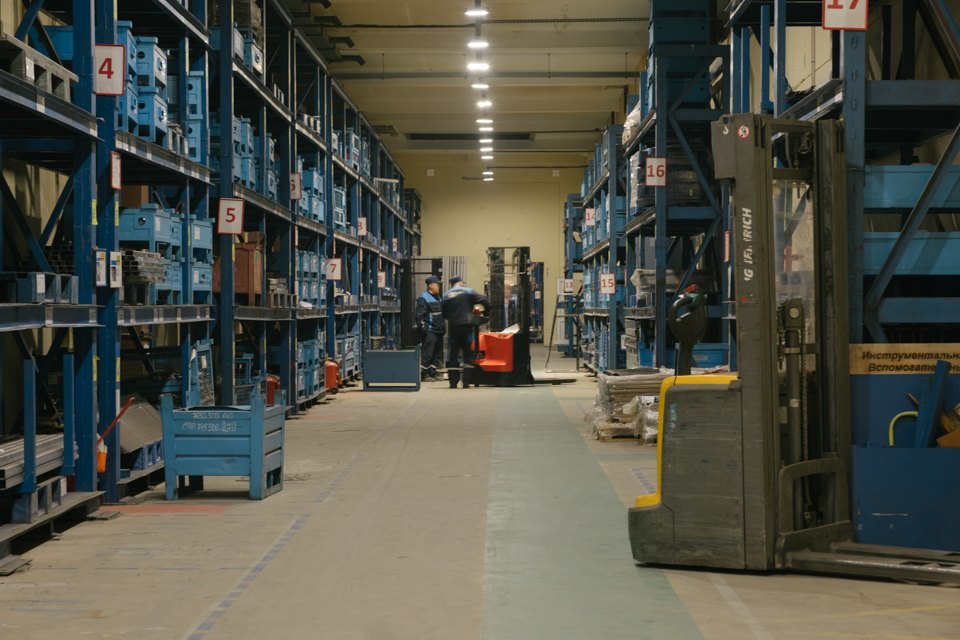
Кузов без колес
Из «колыбели» выходит еще не вагон — пока это только отдельные детали и элементы боковины, которые едут в следующий цех изготовления кузовов. Он кажется настоящим кипящим котлом: здесь постоянно слышен звук болгарки, летят искры от сварки, работают станки. Хотя на этом этапе снова помогают роботы-манипуляторы, в этом цехе много рабочих. Нам объяснили это так: автоматизировать процессы сложно, так как на заводе в разные дни производят разные вагоны, а иногда они даже встречаются на соседних линиях. Так как задачи постоянно меняются в соответствии с модификацией вагонов, то роботизированное оборудование приходится перенастраивать. Пока идет перенастройка, за работу берутся сотрудники цеха сварки. Также их труд необходим, когда нужно доварить в сложнодоступных местах.
На первом посту цеха изготовления кузовов собирают боковину вагона — ее части приваривают друг к другу с помощью роботизированного сварочного комплекса. Работникам помогает кантователь: он вращает раму вокруг своей оси для того, чтобы части было удобно сваривать. Сначала рама собирается на платформе, сваривается с одной стороны, затем переворачивается и сваривается уже с другой.
Дальше собирают торцевые стены и крышу. Из отдельных частей формируют кузов. С помощью распорных рамок на раму вагона приставляют боковины и крышу, выстраивают правильную геометрию, удаляют рамки, приваривают торцевые стенки — и вагон, уже получивший знакомую форму, можно отправлять дальше. На следующем посту нужно приварить к нему пол и установить часть внутрисалонных крепежей — на них будут держаться элементы интерьера.
После сварочных работ кузов ждет зачистка, рихтовка — и переезд в цех дробеструйной обработки и окраски вагонов. Колес у вагона пока нет — колесные тележки параллельно собирают в сварочно-сборочном цеху. Так что на этой стадии вагон по цехам перемещают на специальных платформах, а между цехами — с помощью трансбордера, то есть большой самоходной тележки. Трансбордер выезжает на улицу (для этого у него специально предусмотрена крыша, чтобы на вагон не попадали дождь и снег), движется он перпендикулярно зданию завода, подъезжает к нужному цеху, и вагон перетягивают в цех. Еще несколько вагонов пока ждут своей очереди на следующие операции.
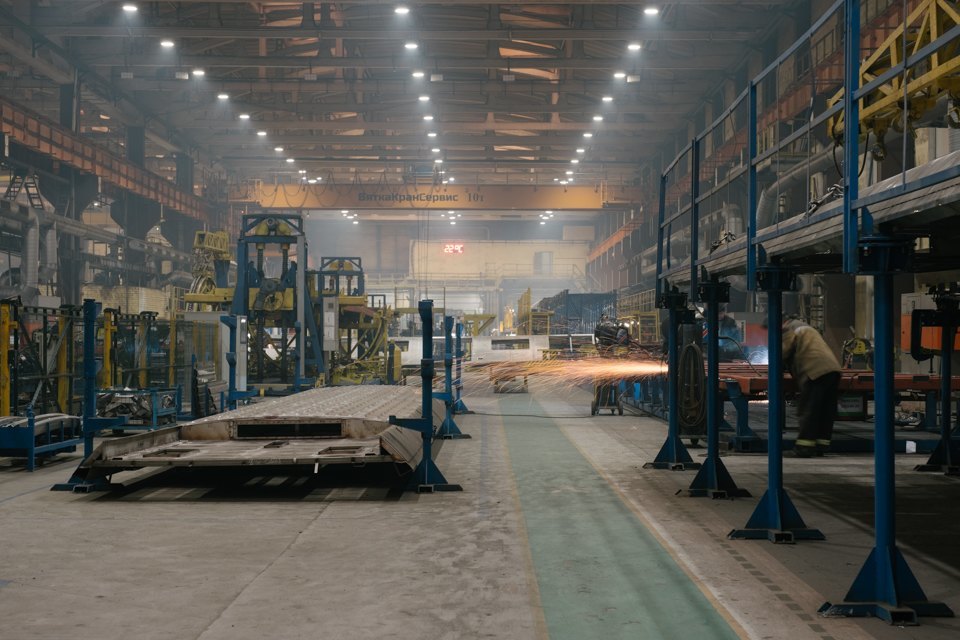
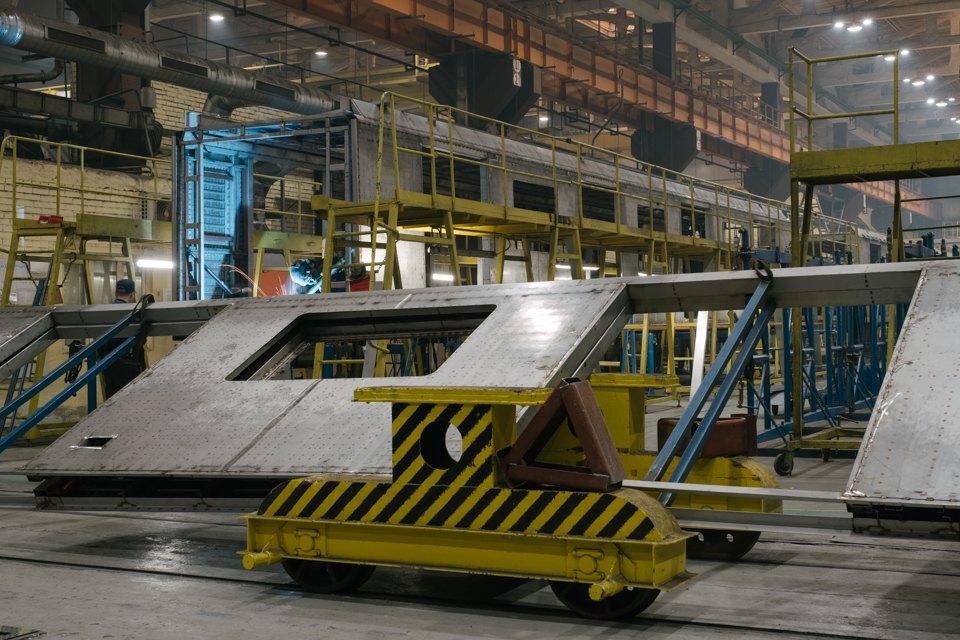
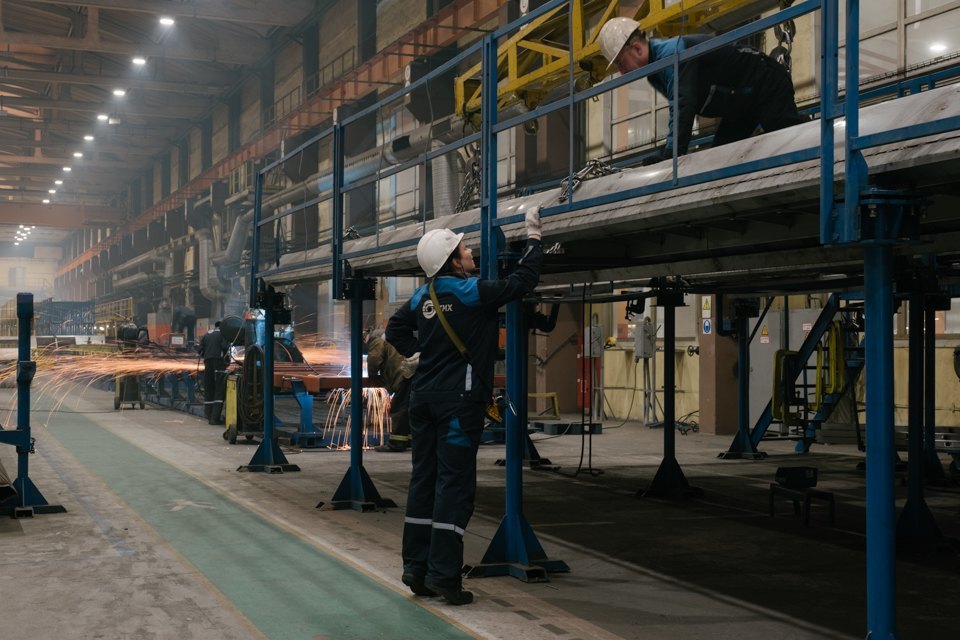
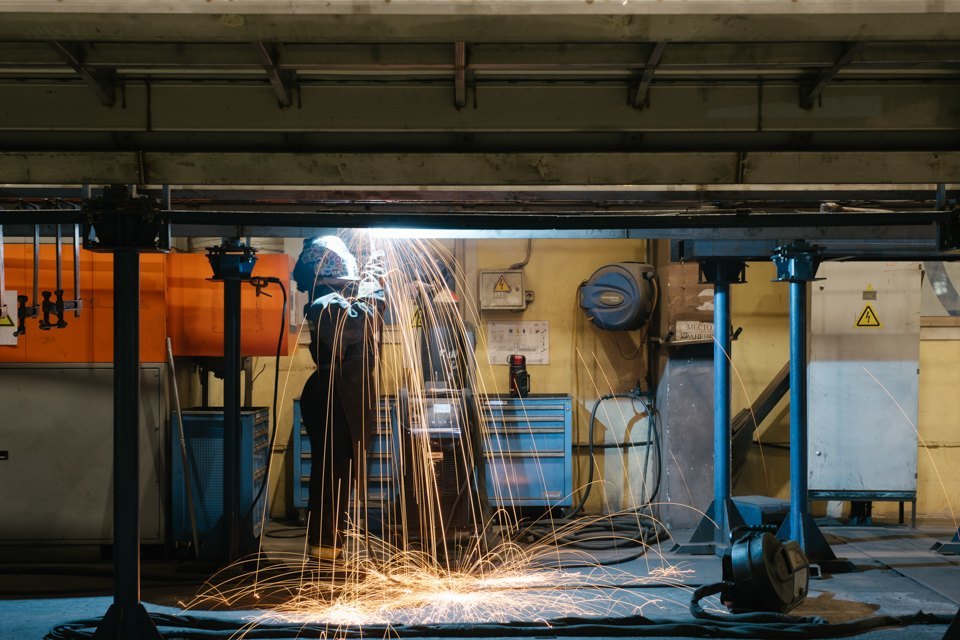
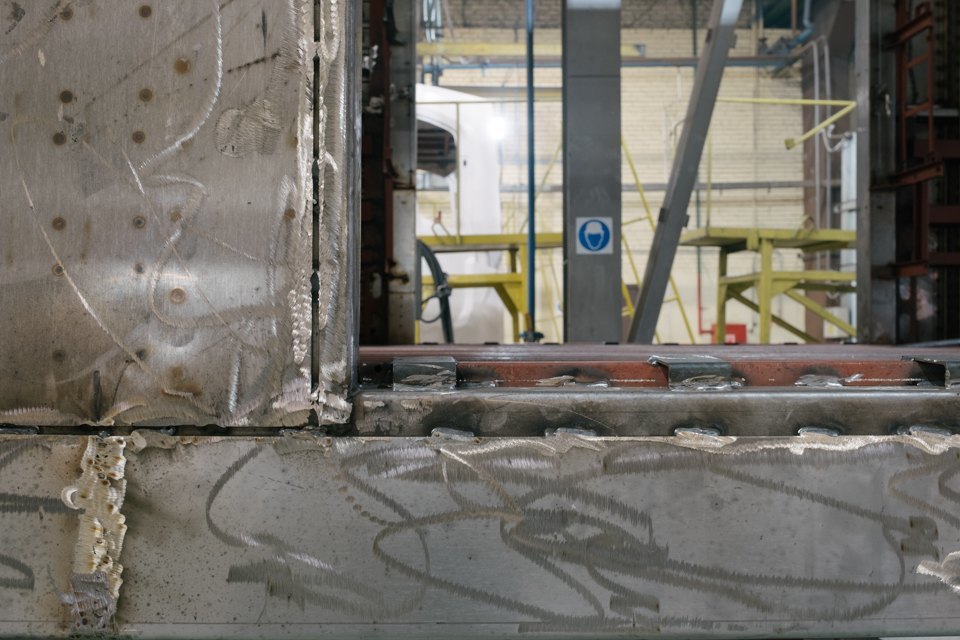
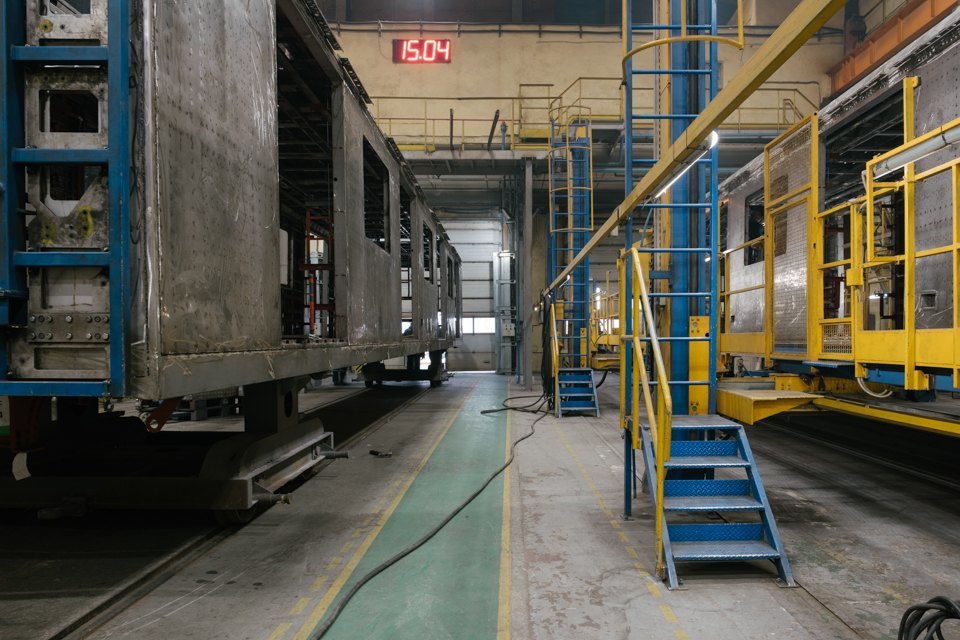
Краска под дождем
В цехе окраски вагонов три камеры — подготовки, окраски и сушки. Кузов подвергают дробеструйной обработке (то есть шлифуют с помощью стальных микрочастиц), грунтуют, выравнивают поверхность и заделывают прерывистые швы, чтобы обеспечить герметичность.
Следующий этап — проверка кузова на герметичность в дождевальной камере. Все технологические отверстия закрывают заглушками, кузов загоняют в камеру, где на него из нескольких сотен форсунок под давлением льется вода. В это время внутри находятся сотрудники и отслеживают возможные протечки — допускается, чтобы в кузов попало не более 40 миллилитров воды. На каждый квадратный метр в минуту выливается примерно десять литров воды: если вагон выдержит такой тропический дождь, то и обычный московский ему будет не страшен. Во второй раз в дождевальную камеру попадает уже окрашенный вагон, а в третий — в собранном виде. Так проверяют герметичность не кузова, а установленных на него элементов — дверей, окон и кондиционеров.
Потом вагон ждет второй слой грунта и окрашивание в цвета, выбранные заказчиком: например, московская ливрея — белая с фирменным узором Московского транспорта. Окрашенный и прошедший испытание водой кузов отправляется в сборочный цех. Здесь он движется от поста к посту, и на каждом на него что-то устанавливают — черновые полы, окна, надверные кожухи, начинают монтаж подвагонного оборудования. На следующих постах — двери, салонные жгуты, воздуховоды, шумоизоляцию, компрессор. Дальше — основное подвагонное оборудование, освещение, пластиковые элементы интерьера. Когда все электромонтажные операции закончены, наступает этап пробоя — проверки работы электрических цепей. Ее нужно выполнить, пока дорогостоящие блоки еще не подключены, чтобы неисправность при подаче напряжения их не испортила.
На следующем посту вагон приобретает вид, знакомый большинству пассажиров, чаще рассматривающих его изнутри, а не снаружи. Рабочие заканчивают монтаж салона, устанавливают диваны, поручни и мониторы, а вагон опускают на подвагонные тележки — теперь не технологические, а настоящие. Они и приводят поезд в движение.
Вагон снова отправляется в дождевальную камеру на проверку герметичности, а после — на обкатку, то есть проверку работы всего оборудования, и сборку состава. С момента захода в цех листа металла до его выхода с линии готового вагона проходит 72 дня. Каждый день на заводе производят два вагона, то есть московский восьмивагонный состав собирается примерно за неделю.
Дальше поезд проходит все необходимые проверки на соответствие требованиям в цехе приемо-сдаточных испытаний. На основе этих испытаний поезд получает разрешение на транспортировку. В этом же цеху производится обкатка готового состава на внутрицеховых железнодорожных путях. После всех проверок поезд цепляют к тепловозу и везут в депо метрополитена. После наладки в депо состав должен проехать по линии без пассажиров 300 километров, и только если он прошел их без единого сбоя, его пускают в эксплуатацию.
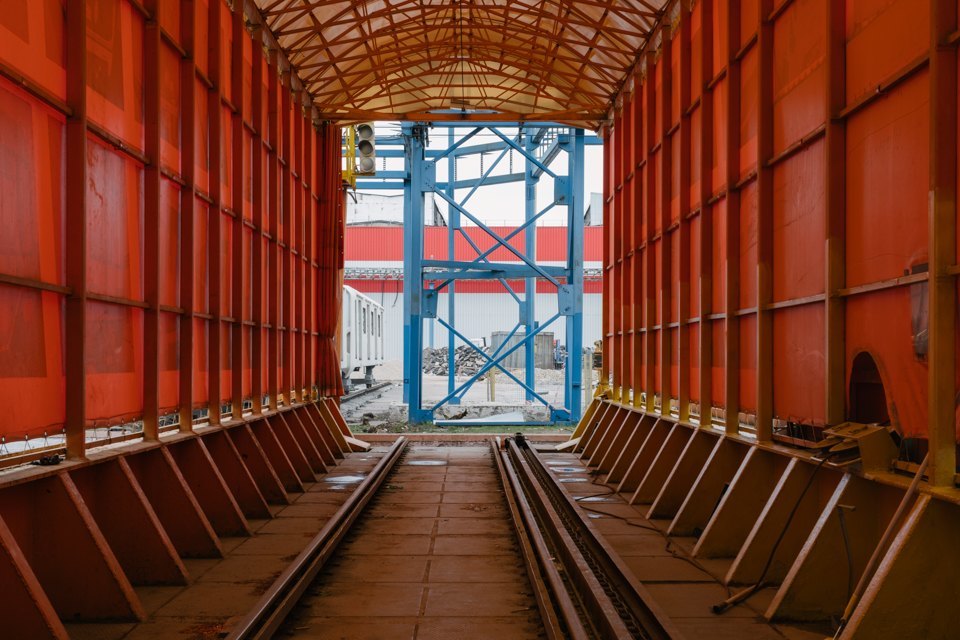
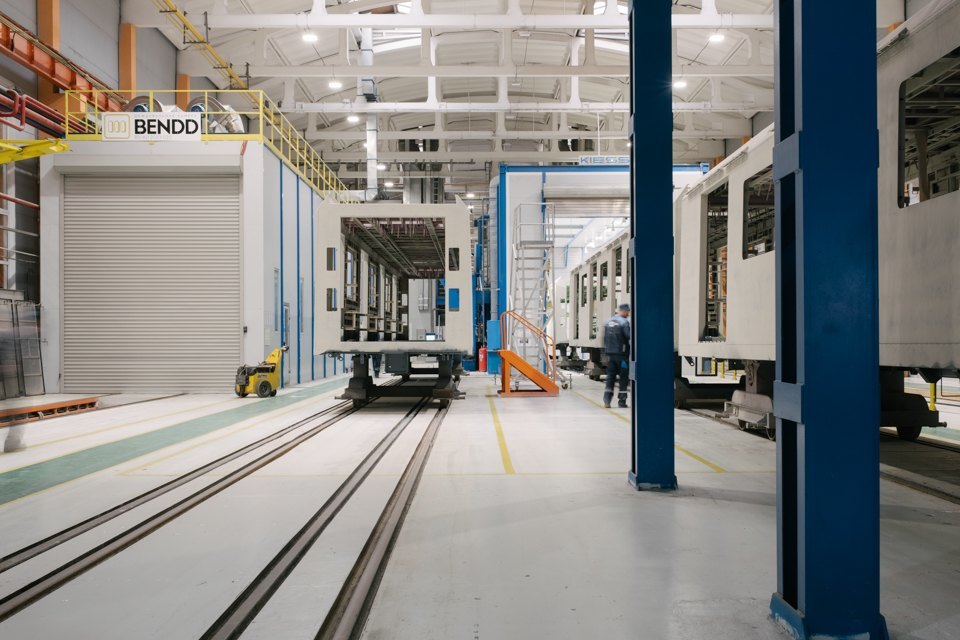
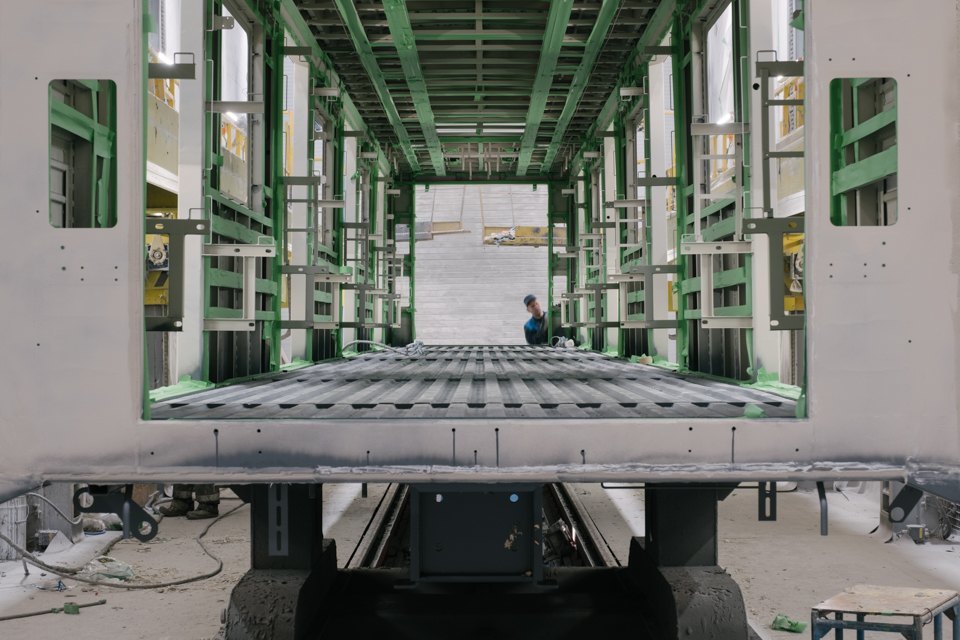
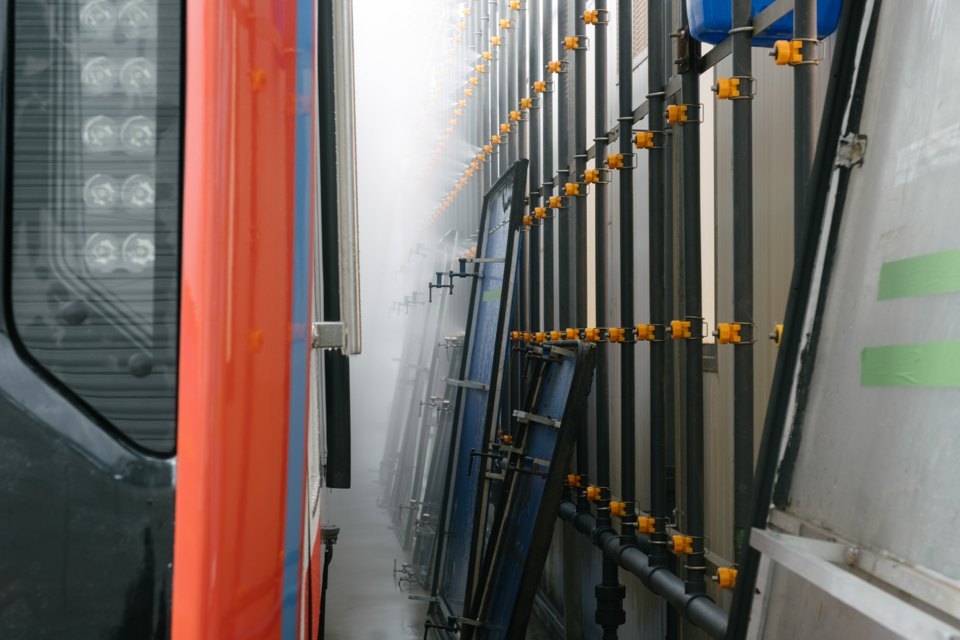
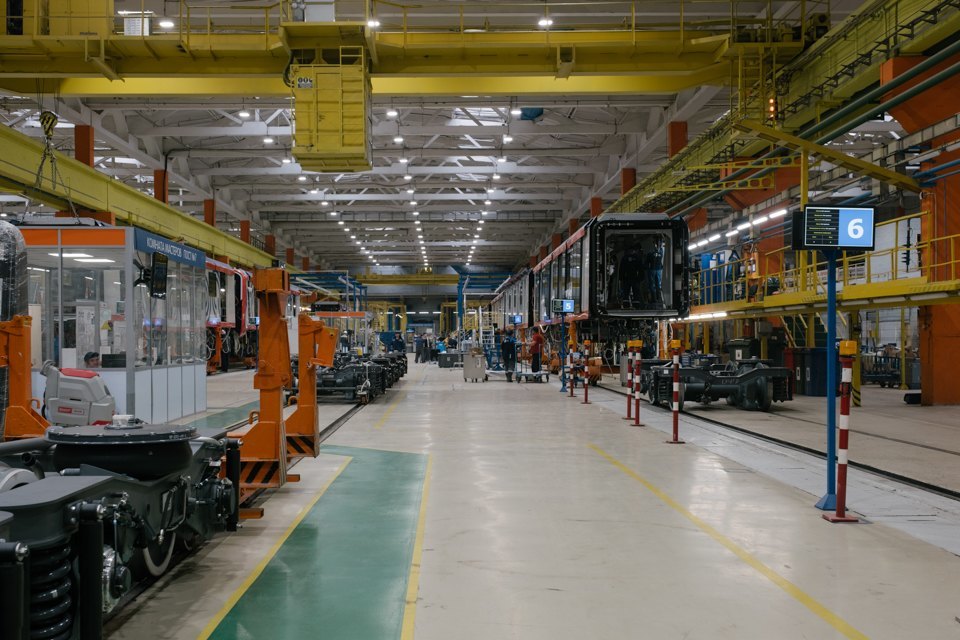
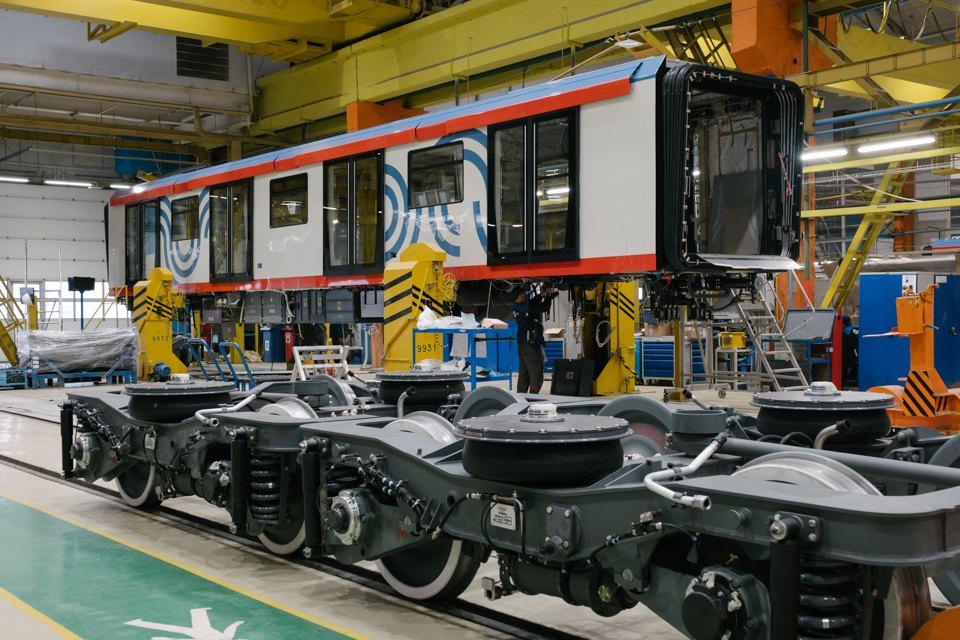
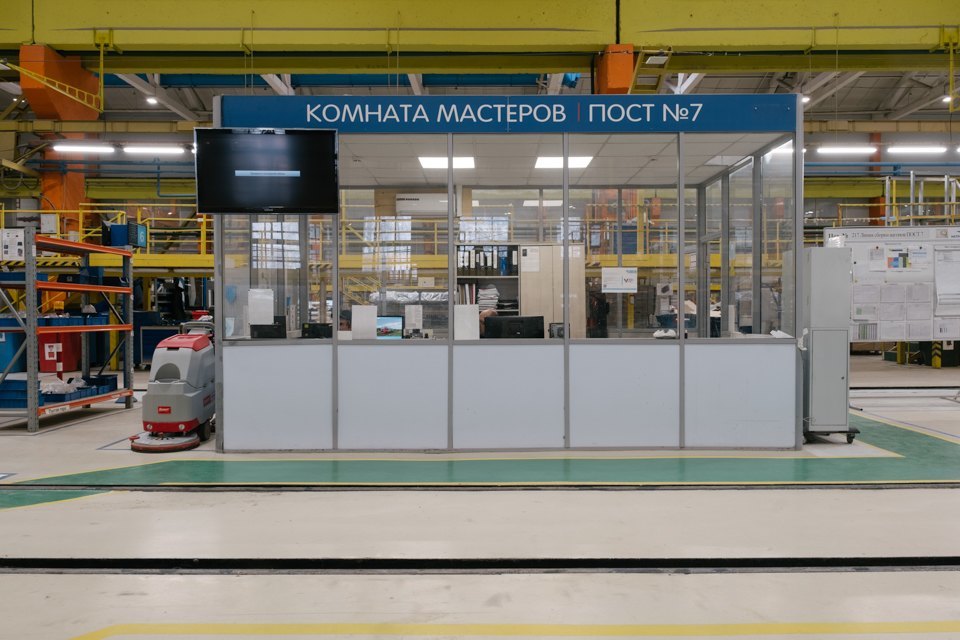
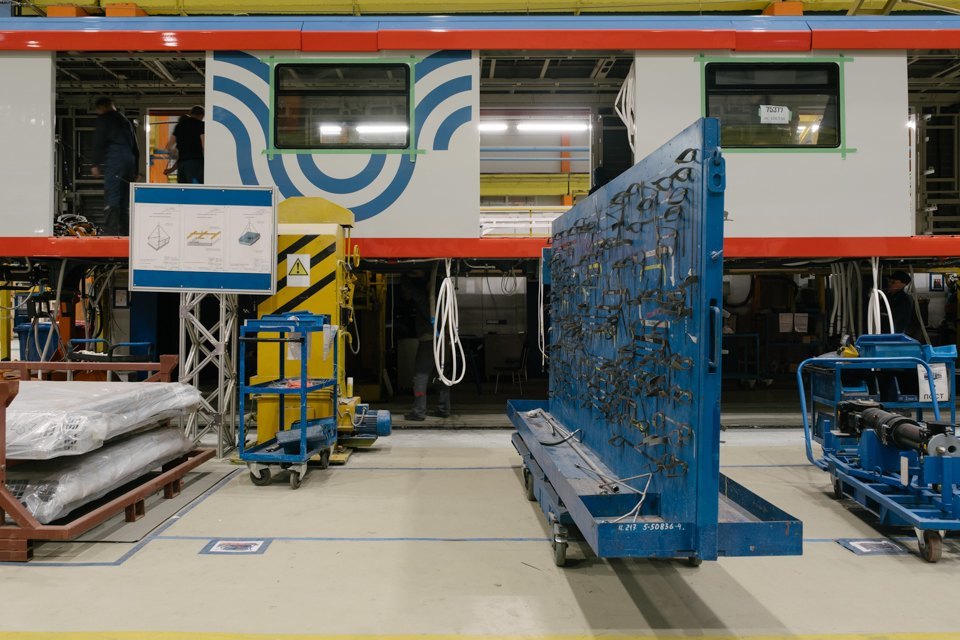
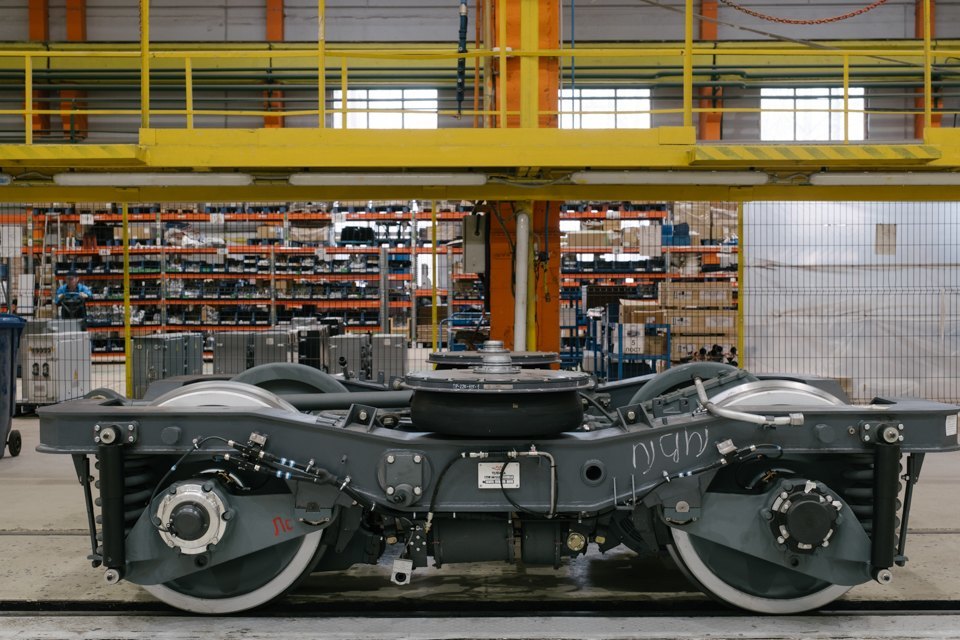
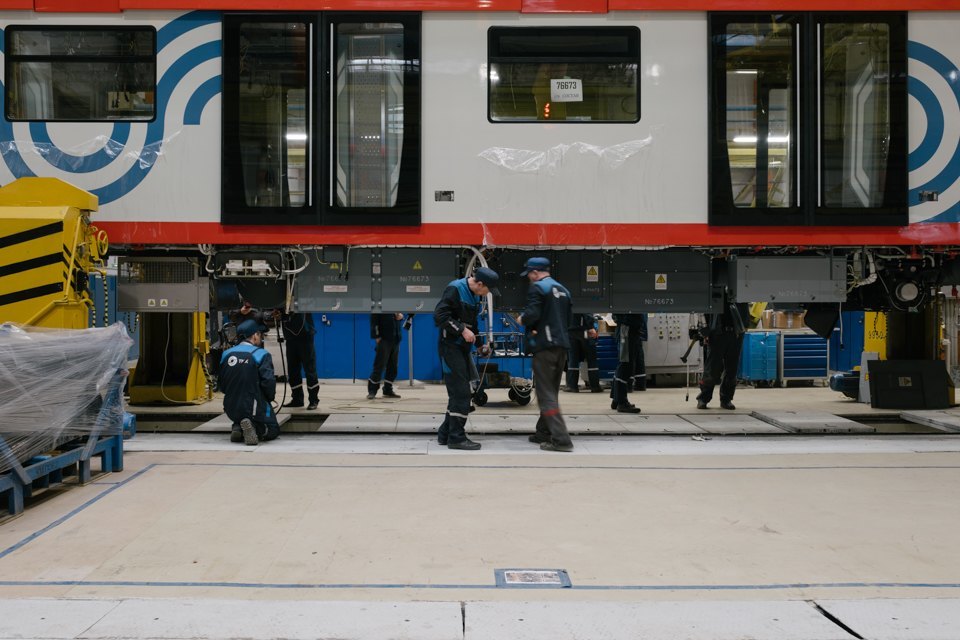
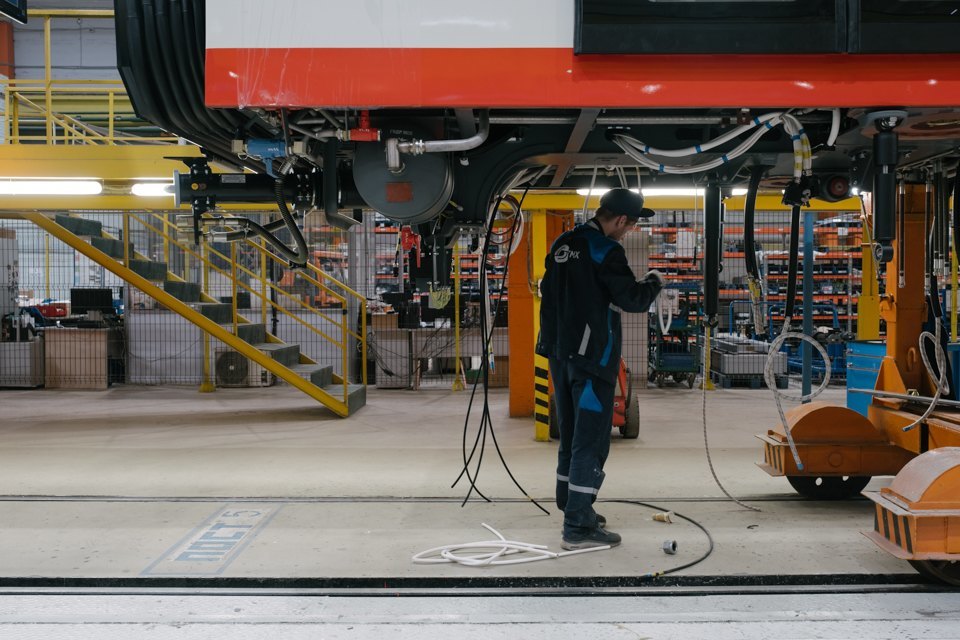
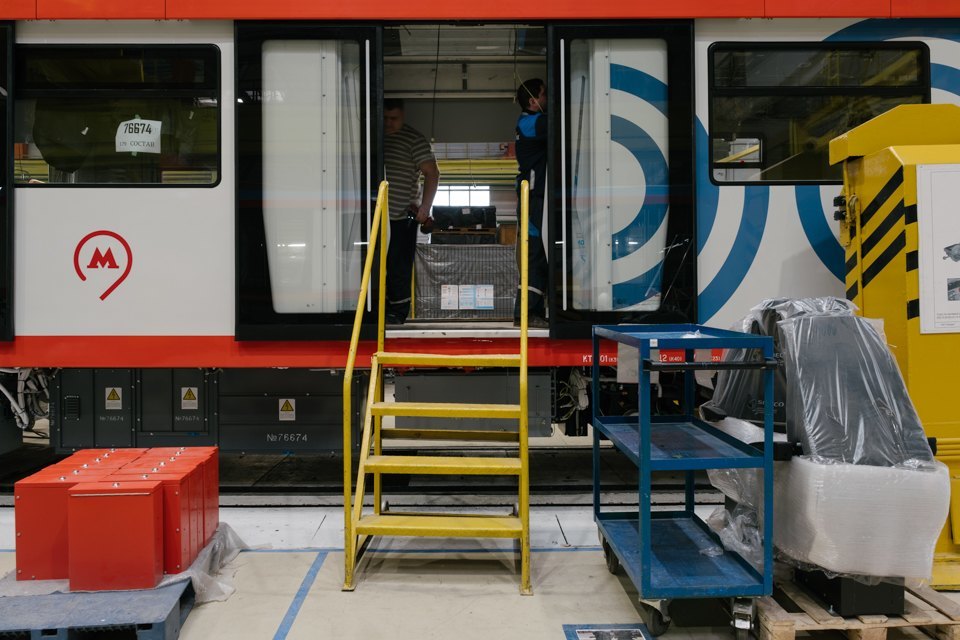
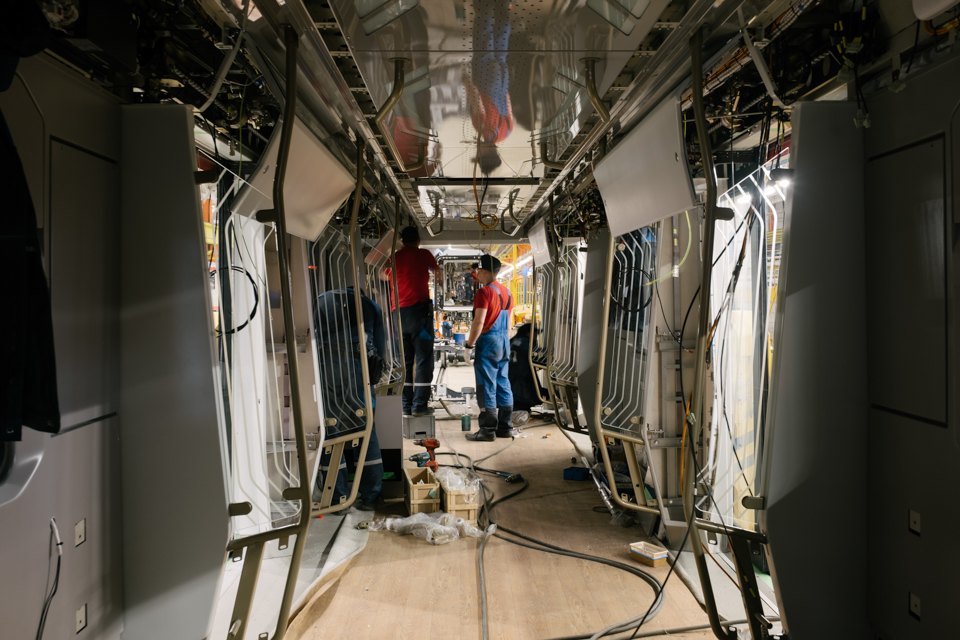
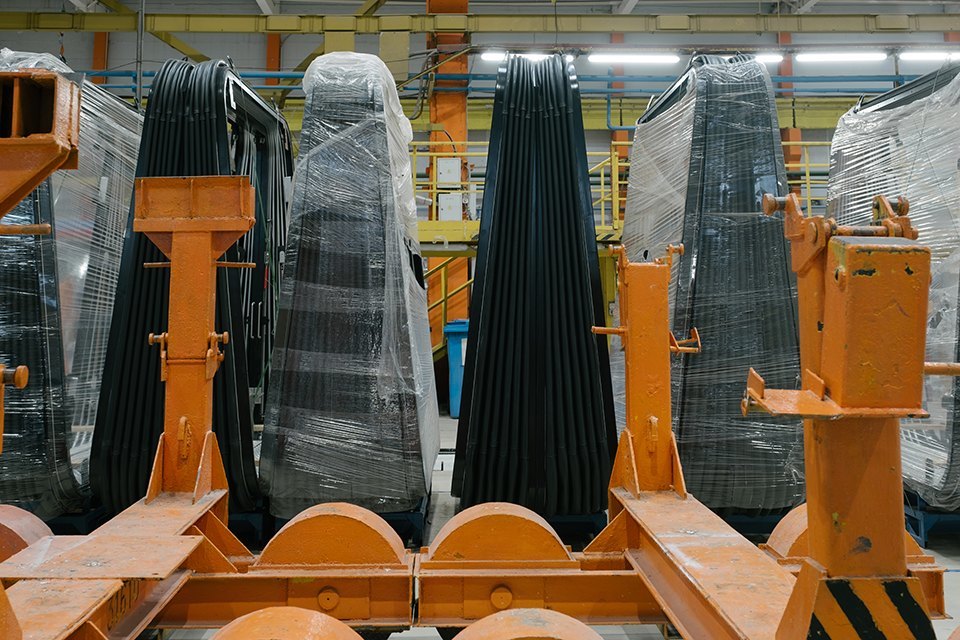
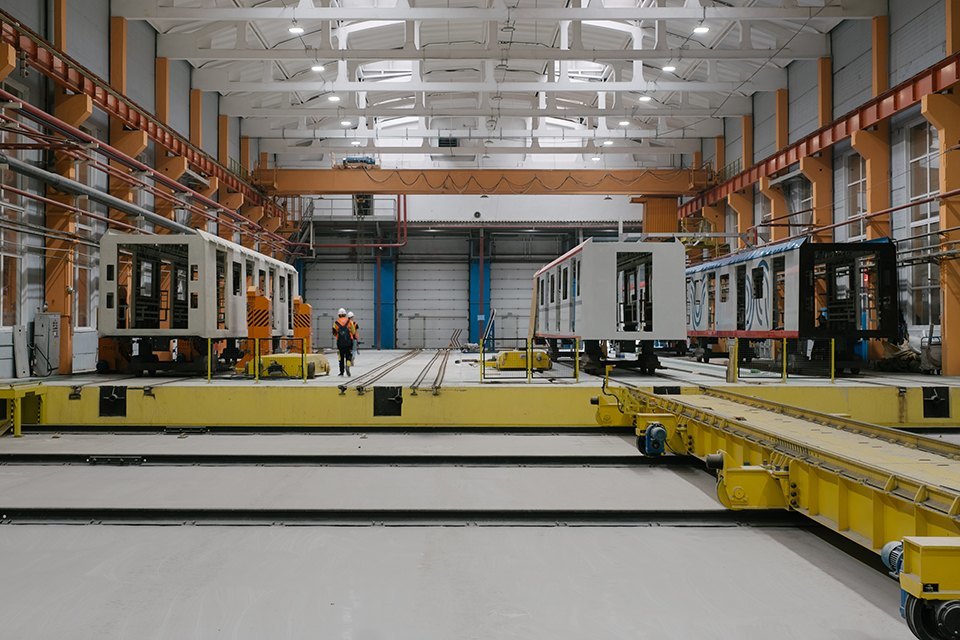